NDE On Welds
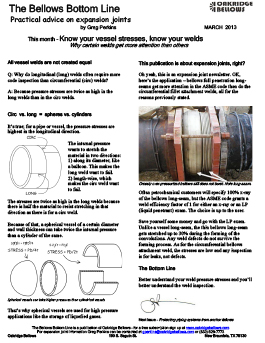
All vessel welds are not created equalQ: Why do longitudinal (long) welds often require more code inspection than circumferential (circ) welds?
A: Because pressure stresses are twice as high in the long welds than in the circ welds.
Circ vs. long = spheres vs. cylinders
It’s true; for a pipe or vessel, the pressure stresses are highest in the longitudinal direction. The internal pressure wants to stretch the
material in two directions:
1) along its diameter, like a balloon. This makes the long weld want to fail.
2) length-wise, which makes the circ weld want to fail.
The stresses are twice as high in the long welds because there is half the material to resist stretching in that direction as there is for a circ weld.
Because of that, a spherical vessel of a certain diameter and wall thickness can take twice the internal pressure than a cylinder of the same.
Spherical vessels can take higher pressures than cylindrical vessels. That’s why spherical vessels are used for high pressure applications like the storage of liquefied gases.
This publication is about expansion joints, right?
Oh yeah, this is an expansion joint newsletter. OK, here’s the application – bellows full penetration long seams get more attention in the ASME code than do the circumferential fillet attachment welds, all for the reasons previously stated. Grossly over-pressurized bellows still does not burst. Note long-seam. Often petrochemical customers will specify 100% x-ray of the bellows long-seam, but the ASME code grants a weld efficiency factor of 1 for either an x-ray or an LP (liquid penetrant) exam. The choice is up to the user.
Save yourself some money and go with the LP exam. Unlike a vessel long-seam, the thin bellows long-seam gets stretched up to 30% during the forming of the convolutions. Any weld defects do not survive the forming process. As for the circumferential bellows attachment weld, the stresses are low and any inspection is for leaks, not defects.
The Bottom Line
Better understand your weld pressure stresses and you’ll better understand the weld inspection.