Why Stainless Steel Doesn’t Rust
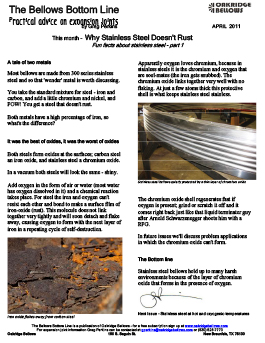
A tale of two metals
Most bellows are made from 300 series stainless steel and so that ‘wonder’ metal is worth discussing.
You take the standard mixture for steel – iron and carbon, and add a little chromium and nickel, and POW! You get a steel that doesn’t rust.
Both metals have a high percentage of iron, so what’s the difference?
It was the best of oxides, it was the worst of oxides
Both steels form oxides at the surfaces; carbon steel an iron oxide, and stainless steel a chromium oxide.
In a vacuum both steels will look the same – shiny.
Add oxygen in the form of air or water (most water has oxygen dissolved in it) and a chemical reaction takes place. For steel the iron and oxygen can’t resist each other and bond to make a surface film of iron-oxide (rust). This molecule does not link together very tightly and will soon detach and flake away, causing oxygen to form with the next layer of iron in a repeating cycle of self-destruction.
Apparently oxygen loves chromium, because in stainless steels it is the chromium and oxygen that are soul-mates (the iron gets snubbed). The chromium oxide links together very well with no flaking. At just a few atoms thick this protective shell is what keeps stainless steel stainless.
The chromium oxide shell regenerates fast if oxygen is present; grind or scratch it off and it comes right back just like that liquid terminator guy after Arnold Schwarzenegger shoots him with a RPG.
In future issues we’ll discuss problem applications in which the chromium oxide can’t form.
The Bottom line
Stainless steel bellows hold up to many harsh environments because of the layer of chromium oxide that forms in the presence of oxygen.