Cryogenic Properties of Stainless Steel Bellows
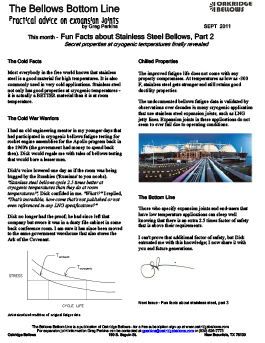
The Cold Facts
Most everybody in the free world knows that stainless steel is a good material for high temperatures. It is also commonly used in very cold applications. Stainless steel not only has good properties at cryogenic temperatures – it is actually a BETTER material than it is at room temperature.
The Cold War Warriors
I had an old engineering mentor in my younger days that had participated in cryogenic bellows fatigue testing for rocket engine assemblies for the Apollo program back in the 1960’s (the government had money to spend back then). Dick would regale me with tales of bellows testing that would bore a lesser man.
Dick’s voice lowered one day as if the room was being bugged by the Russkies (‘Russians’ to you noobs). “Stainless steel bellows cycle 2.5 times better at cryogenic temperatures than they do at room temperatures!”, Dick confided in me. “What!?” I replied, “That’s incredible, how come that’s not published or not even referenced in any LNG specifications?”
Dick no longer had the proof; he had since left that company but swore it was in a dusty file cabinet in some back conference room. I am sure it has since been moved to the same government warehouse that also stores the Ark of the Covenant. Artist simulated rendition of original fatigue data
Chilled Properties
The improved fatigue life does not come with any property compromises. At temperatures as low as -300 F, stainless steel gets stronger and still retains good ductility properties.
The undocumented bellows fatigue data is validated by observations over decades in many cryogenic application that use stainless steel expansion joints, such as LNG jetty lines. Expansion joints in these applications do not seem to ever fail due to operating conditions.
The Bottom Line
Those who specify expansion joints and end-users that have low temperature applications can sleep well knowing that there is an extra 2.5 times factor of safety that is above their requirements.
I can’t prove that additional factor of safety, but Dick entrusted me with this knowledge; I now share it with you and future generations.