Insider Secrets To Expansion Joint Repair
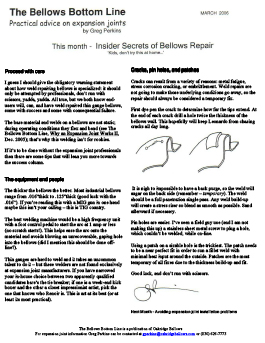
Proceed with care
I guess I should give the obligatory warning statement about how weld repairing bellows is specialized: it should only be attempted by professionals, don’t run with scissors, yadda, yadda. All true, but we both know end-users will, can, and have weld repaired thin gauge bellows, some with success and some with consequential failure.
The base material and welds on a bellows are not static; during operating conditions they flex and bend (see The Bellows Bottom Line, Why an Expansion Joint Works II, Dec. 2005); that’s why this welding isn’t for rookies.
If it’s to be done without the expansion joint professionals then there are some tips that will lean you more towards the success column.
The equipment and people
The thicker the bellows the better. Most industrial bellows range from .016”thick to .125”thick (good luck with the .016”). If you’re reading this with a MIG gun in one hand maybe this isn’t your calling – this is TIG country.
The best welding machine would be a high frequency unit with a foot control pedal to start the arc at 1 amp or less (no scratch starts!). This helps ease the arc onto the material and avoids blowing an unrecoverable, gaping hole into the bellows (did I mention this should be done off-line?).
Thin gauges are hard to weld and it takes an uncommon talent to do it – but these welders are not found exclusively at expansion joint manufacturers. If you have narrowed your in-house choice between two apparently qualified candidates here’s the tie breaker; if one is a week-end kick boxer and the other a closet impressionist artist, pick the one that knows who Renoir is. This is art at its best (or at least its most practical).
Cracks, pin holes, and patches
Cracks can result from a variety of reasons: metal fatigue, stress corrosion cracking, or embrittlement. Weld repairs are not going to make those underlying conditions go away, so the repair should always be considered a temporary fix.
First dye pen the crack to determine how far the tips extend. At the end of each crack drill a hole twice the thickness of the bellows wall. This hopefully will keep Leonardo from chasing cracks all day long.
It is nigh to impossible to have a back purge, so the weld will sugar on the back side (remember – temporary). The weld should be a full penetration single pass. Any weld build-up will create a stress riser so blend as smooth as possible. Sand afterward if necessary.
Pin holes are easier. I’ve seen a field guy use (and I am not making this up) a stainless sheet metal screw to plug a hole, which couldn’t be welded, while on-line.
Using a patch on a sizable hole is the trickiest. The patch needs to be a near perfect fit in order to run a fillet weld with minimal heat input around the outside. Patches are the most temporary of all fixes due to the thickness build-up and fit.
Good luck, and don’t run with scissors.