625 vs 625 LCF Bellows Performance
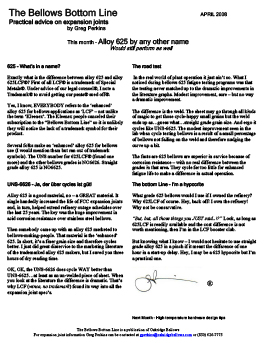
625 – What’s in a name?
Exactly what is the difference between alloy 625 and alloy 625LCF®? First of all LCF® is a trademark of Special Metals®. Under advice of our legal counsel®, I note a Trademark® to avoid getting our pants® sued off®.
Yes, I know, EVERYBODY refers to the ‘enhanced’ alloy 625 for bellows applications as ‘LCF’ – not unlike the term ‘Kleenex’. The Kleenex people canceled their subscription to the “Bellows Bottom Line” so it is unlikely they will notice the lack of a trademark symbol for their product.
Several folks make an ‘enhanced’ alloy 625 for bellows use (I would mention them but ran out of trademark symbols). The UNS number for 625LCF® (found one more) and the other bellows grades is NO6626. Straight grade alloy 625 is NO6625.
UNS-6626 – Ja, der über cycles ist güt!
Alloy 625 is a good material, no – a GREAT material. It single handedly increased the life of FCC expansion joints and, in turn, helped extend refinery outage schedules over the last 25 years. The key was the huge improvement in acid corrosion resistance over stainless steel bellows.
Then somebody came up with an alloy 625 marketed to bellows-making-people. That material is the ‘enhanced’ 625. In short, it’s a finer grain size and therefore cycles better. I just did great disservice to the marketing literature of the trademarked alloy 625 makers, but I saved you three hours of dry reading time.
OK, OK, the UNS-6626 does cycle WAY better than UNS-6625…at least as an un-welded piece of sheet. When you look at the literature the difference is dramatic. That’s why LCF (wince, no trademark) found its way into all the expansion joint spec’s.
The road test
In the real world of plant operation it just ain’t so. What I noticed during bellows 625 fatigue testing programs was that the testing never matched up to the dramatic improvements in the literature graphs. Modest improvement, sure – but no way a dramatic improvement.
The difference is the weld. The sheet may go through all kinds of magic to get those cycle-happy small grains but the weld ends up as…guess what…straight grade grain size. And ergo it cycles like UNS-6625. The modest improvement seen in the lab when cycle testing bellows is a result of a small percentage of bellows not failing on the weld and therefore nudging the curve up a bit.
The facts are 625 bellows are superior in service because of corrosion resistance – with no real difference between the grades in that area. They cycle far too little for enhanced fatigue life to make a difference in actual operation.
The bottom Line – I’m a hypocrite
What grade 625 bellows would I use if I owned the refinery? Why 625LCF of course. Hey, back off! I own the refinery! Why not be conservative.
“But, but, all those things you JUST said..!?” Look, as long as 625LCF is readily available and the cost difference is not worth mentioning, then I’m in the LCF booster club.
But knowing what I know – I would not hesitate to use straight grade alloy 625 in a pinch if it meant the difference of one hour in a start-up delay. Hey, I may be a 625 hypocrite but I’m a practical one.