More metal bellows repair tips
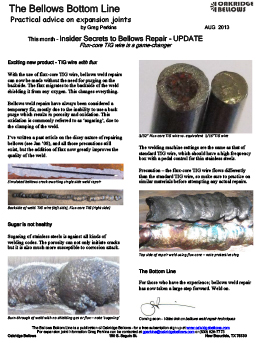
This month – Protecting Piping From Anchor Failures – UPDATE
Exciting new product – TIG wire with flux
With the use of flux-core TIG wire, bellows weld repairs can now be made without the need for purging on the backside. The flux migrates to the backside of the weld shielding it from any oxygen. This changes everything.
Bellows weld repairs have always been considered a temporary fix, mostly due to the inability to use a back purge which results in porosity and oxidation. This oxidation is commonly referred to as ‘sugaring’, due to the clumping of the weld.
I’ve written a past article on the dicey nature of repairing bellows (see Jan ’08), and all those precautions still exist, but the addition of flux now greatly improves the quality of the weld.
Simulated bellows crack awaiting single side weld repair Backside of weld. TIG wire (left side), Flux‐core TIG (right side)
Sugar is not healthy
Sugaring of stainless steels is against all kinds of welding codes. The porosity can not only initiate cracks but it is also much more susceptible to corrosion attack.
Burn‐through of weld with no shielding gas or flux – note ‘sugaring’ 3/32” Flux‐core TIG wire vs. equivalent 1/16”TIG wire The welding machine settings are the same as that of standard TIG wire, which should have a high frequency box with a pedal control for thin stainless steels.
Precaution – the flux-core TIG wire flows differently than the standard TIG wire, so make sure to practice on similar materials before attempting any actual repairs.
Top side of repair weld using flux‐core – note protective slag
The Bottom Line
For those who have the experience; bellows weld repair has now taken a large step forward. Weld on.